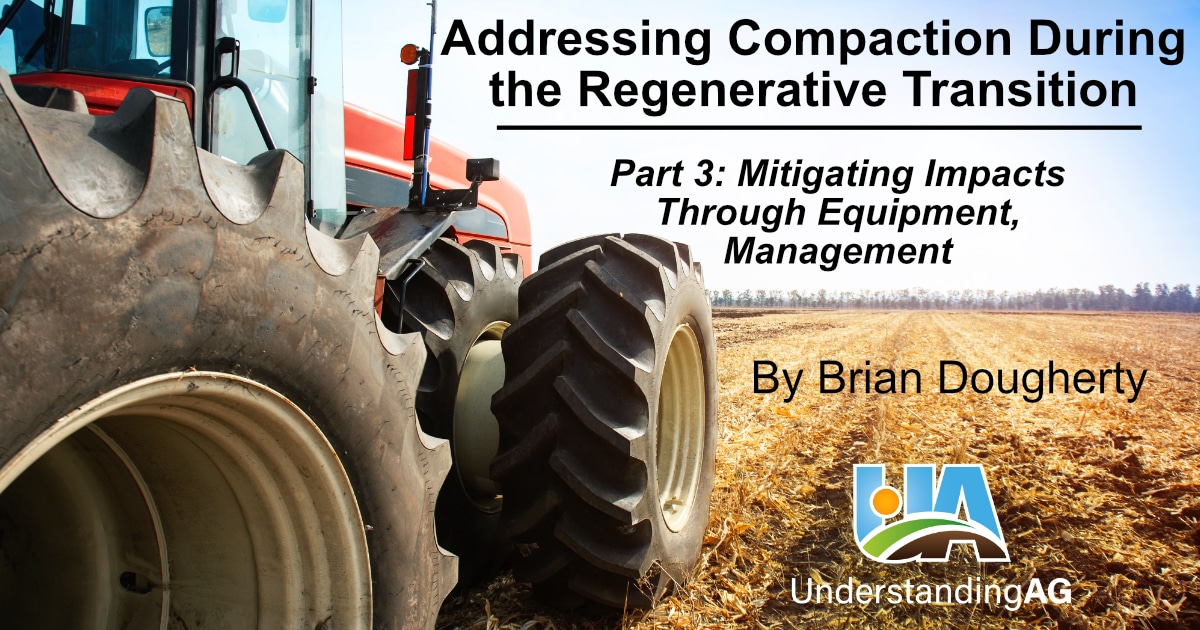
In parts one and two of this series, we reviewed the role of biology and the importance of living roots, aggregated soil, and a functioning water cycle for building strong, compaction-resistant soils. Now let’s look at the equipment and field management practices that can help mitigate compaction while you transition to a regenerative system.
Compaction depth and equipment loads
The depth of a traffic compaction layer depends on several factors. Topsoil compaction (roughly the top 12 inches) is caused by contact pressure. If you are running radial tires, a general rule of thumb is that the soil will experience 1-2 pounds per square inch (psi) more than the air pressure inside your tire. The higher your tire pressure, the smaller the contact area with the ground, and the more compaction it will cause, so keep tire pressures as low as possible for your operating conditions. A larger tire footprint reduces surface compaction but unfortunately it does not reduce the depth of compaction.
Compaction at roughly the 12-20-inch depth is caused by a combination of contact pressure and axle loads. Below that it is primarily an issue of axle loads. Loads greater than 10 tons/axle will cause subsoil compaction in wet conditions. Try to stay below five tons/axle in poorly aggregated soil and 10 tons/axle in well-aggregated soil. Unfortunately, as the table below shows, most modern equipment can easily exceed the recommended axle weights. Single axle grain carts and large combines are the worst offenders, but manure tankers and larger tractors also easily exceed 10 tons/axle. Unloading combines on headlands and/or more frequently can help if fields are wet during harvest.
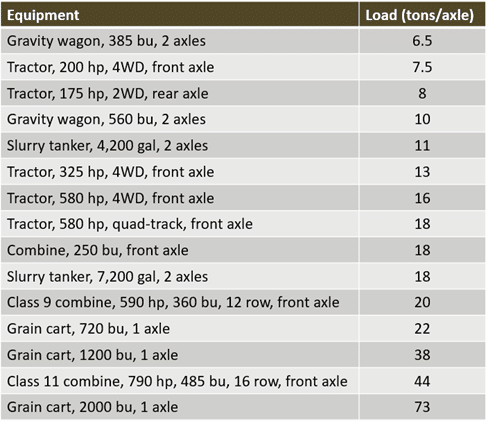
Tires, tracks, and technology
Should you switch to tracks rather than tires? Tracks have several advantages, including a smoother ride, better traction, better flotation, and less slippage. On the downside, they are more expensive and heavier, so they add to your axle load. When it comes to compaction, they are basically “a wash” compared to properly inflated tires. Properly inflated is key. Overinflated tires are much worse than tracks, so run tires at the lowest recommended pressure for the load they are carrying. It seems counterintuitive that tires could be equivalent of tracks when it comes to compaction, but with tracks most of the weight is on the drive and idler wheels and mid-rollers. They create pressure points under the track just like the pressure points under tires.
Switching to larger and/or wider tires will spread out the load and reduce topsoil compaction. Also consider purchasing increased flexion (IF) or very high flexion (VF) tires. They are designed to carry heavier loads at the same pressure as standard radial tires. Another option is a central tire inflation system that allows you to inflate and deflate tires on the go. You can bump up the pressure for traveling down the road at higher speeds when higher pressure is needed, then deflate the tires when you get to the field. These systems reduce compaction and should help improve yields. It is estimated that they can improve fuel economy by about 10% and extend tire life by 20%. However, that benefit comes at a high-purchase cost so you will need to evaluate the tradeoffs.
About 75% of the increase in soil bulk density and 90% of wheel sinkage is caused during the first pass with equipment. An increase in bulk density equals less pore space in the soil. Also, the longer the dwelling time of a load on the soil, the greater the increase in bulk density. Since most of the damage is done on the first pass, it makes sense to continue driving in the same path rather than move over and compact a different area.
Controlled Traffic Farming (CTF) takes advantage of this to mitigate the damage from heavy-axle loads. The system uses permanent tramlines for equipment traffic. The goal is to traffic the smallest percentage of the soil surface as possible. Wheel spacing on all equipment needs to match and all equipment needs to be the same working width or a multiple of that width for CTF to work. Grain carts run in the previous track made by the combine. This system requires significant investment to set up, but research from Australia where the method was pioneered shows average yield increases of about 10%, fuel savings up to 25%, lower horsepower requirements, more efficient chemical and fertility applications, and healthier, less compacted soil. If you are running some of the larger equipment listed in the table above, CTF is worth taking a very serious look at. Even the healthiest soil cannot withstand the axle weights of today’s largest equipment.
How long will it take to repair?
The deeper the compaction goes, the longer it will take to repair. Freeze/thaw cycles are not very effective at repairing compaction. It takes multiple cycles to break compacted layers and the deeper you go in the profile, the less often it freezes. Topsoil compaction will generally cause a more significant yield loss relative to subsoil compaction, but it can be fixed relatively quickly. With living roots you can typically get rid of topsoil compaction within about five years. Compaction in the 12- 24-inch depth range might take 10 years or longer. Subsoil compaction below 24 inches can take decades to repair. Depending on the severity – for example 30+ ton axle loads on poorly structured soil in wet conditions – it’s safe to assume it will be there long after you have moved on to greener pastures.
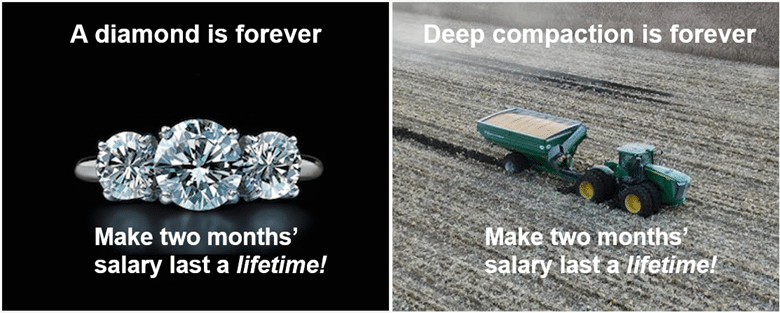
Do yourself a favor and spend a lifetime with your significant other, not your compaction. If you keep a living root in the ground to build and maintain aggregates, fix your water cycle, and manage equipment and field traffic to minimize damage, you will be well on your way to healthy soil and a smoother transition to a regenerative farming system. Thanks for sticking with it and best of luck!